POLMAK, First and most experienced diamond
tool manufacturer in Turkey.
PRODUCTS OF POLMAK,
·
Diamond Circular Saws
·
Frame Saw
Blades
·
Diamond Core Drills
·
Diamond Milling Tools, Grinders and
Profiles
POLMAK MAKİNE İMALAT A.Ş.
Head
Office : Büklüm Sk. No: 94, Kavaklıdere 06700 – ANKARA
Tel: +90 (312) 426 62 66 – 426
66 79 – 426 61 72 - Fax: +90 (312) 468 37 03
Factory
: Esenboğa Yolu 19. Km. Çubuk – ANKARA
Tel: +90 (312) 398 04 28
İstanbul
Office : Tel: +90 (212) 659 19 27 - Fax: +90 (212) 659 41
29
İzmir
Office : Tel: +90 (232) 482 11 15 - Fax: +90 (232) 482
11 15
Mersin
Office : Tel: +90 (324) 221 51 44 - Fax: +90 (324) 221 54
84
Afyon Office (Iscehisar)
: Tel: +90 (272) 341 35 47
PERIPHERAL SPEED
The peripheral speed for
diamond saw blades should lie between 20 to 65 meters per second depending
on the hardness and abrasiveness of the material to be sawn.
Table 1 shows the
recommended peripheral speeds for different materials, and table 2 shows the
motor rpm needed to obtain required peripheral speed.
TABLE 1
Material Peripheral Speed
m/sec
Hard compact materials like 20-30
Granite, porphyry, diabase,
Refractory bricks, etc.
Medium hard and compact 20-50
Materials like marble, serpentinite,
Soft granite, sandstone etc.
Abrasive materials like soft 50-65
Sandstone travertine, etc.
Lower peripheral speed will
accelerate the wear, higher peripheral speed will result in less cutting
power.
CUTTING SPEED
Cutting speed is the quantity of material sawn during a certain time period
and generally expressed as cm2/min. Peripheral speed, together with the rate
of feed determines the cutting speed. Maximum performance is only possible
with the right cutting speed. Cutting speed of a circular saw blade in
marble should be about 500 cm2/min.
An excessively high cutting
speed will cause premature wear by tearing out the diamond particles whereas
excessively low cutting speeds will cause the diamond particles to become
shiny and not penetrate into the stone sufficiently.
FLANGES
Flange diameter depends on the blade diameter (see Table 3 for recommended
flange diameters).
Flanges must be free of
rust, dirt, grease, and deformation. Flange rims must be seated well and
bolts secured tight. |
MOUNTING OF SAW BLADES
An arrow on the blade disc
shows the rotation direction. It is important not to make a mistake in the
direction where frequent dismantling is necessary.
CUTTING IN STEPS
Hard materials like
granite, diabase, porphyry, porcelaine, etc., should be cut in steps. If the
saw tends to loose its cutting speed, the depth of the step should be
reduced and the feed should be increased.
FLUSHING WATER
It is important to have effective flushing of the cuttings and cooling of
the segments. Sufficient quantity of flushing water should be applied to
both faces of the disc at a point near the flanges.
The pressure of the
flushing water is not important so long the quantity is sufficient (see
Table 3 for recommended water flow).
MACHINE
Sawing machine should be robust and free from vibrations. Vibration
increases the wear of segments.
Motor must be of sufficient power (see Table 3 for recommended motor powers).
-
The
table should be positioned exactly parallel to the saw blade and there
should not be any deviation. Otherwise abnormal wear will result on the
blade and the cut will be uneven and splintered.
The bore of the disc should
fit the spindle tightly, and the shaft should be centered. |
2. MOTOR RPM
NEEDED TO OBTAIN REQUIRED PERIPHERAL SPEED
DIA,
mm |
PERIPHERY SPEED (m/sec) |
25 |
30 |
35 |
40 |
45 |
50 |
55 |
60 |
65 |
250 |
1910 |
2290 |
2680 |
3060 |
3440 |
3820 |
4200 |
4590 |
4970 |
300 |
1590 |
1910 |
2230 |
2550 |
2870 |
3190 |
3500 |
3820 |
4140 |
350 |
1370 |
1640 |
1910 |
2180 |
2460 |
2730 |
3000 |
3280 |
3550 |
400 |
1190 |
1430 |
1670 |
1910 |
2150 |
2390 |
2630 |
2870 |
3100 |
450 |
1060 |
1270 |
1490 |
1700 |
1910 |
2120 |
2330 |
2550 |
2760 |
500 |
950 |
1150 |
1340 |
1530 |
1720 |
1910 |
2100 |
2290 |
2480 |
550 |
900 |
1000 |
1200 |
1400 |
1600 |
1700 |
1900 |
2100 |
2200 |
600 |
800 |
950 |
1110 |
1280 |
1430 |
1590 |
1750 |
1910 |
2070 |
650 |
730 |
880 |
1030 |
1180 |
1320 |
1470 |
1620 |
1760 |
1910 |
700 |
680 |
820 |
950 |
1090 |
1230 |
1360 |
1500 |
1640 |
1780 |
800 |
600 |
700 |
850 |
950 |
1050 |
1200 |
1350 |
1450 |
1550 |
850 |
560 |
670 |
790 |
900 |
1010 |
1120 |
1240 |
1350 |
1460 |
900 |
530 |
640 |
740 |
850 |
950 |
1060 |
1170 |
1270 |
1380 |
1000 |
480 |
570 |
670 |
760 |
860 |
950 |
1050 |
1150 |
1240 |
1100 |
430 |
520 |
610 |
690 |
780 |
870 |
950 |
1040 |
1130 |
1200 |
400 |
480 |
560 |
640 |
720 |
800 |
880 |
950 |
1030 |
1300 |
370 |
440 |
510 |
590 |
660 |
730 |
800 |
880 |
950 |
1400 |
340 |
410 |
480 |
550 |
610 |
680 |
750 |
820 |
890 |
1600 |
300 |
360 |
420 |
480 |
540 |
600 |
660 |
720 |
780 |
1800 |
260 |
320 |
370 |
420 |
480 |
530 |
580 |
640 |
690 |
2000 |
240 |
290 |
330 |
380 |
430 |
480 |
520 |
570 |
620 |
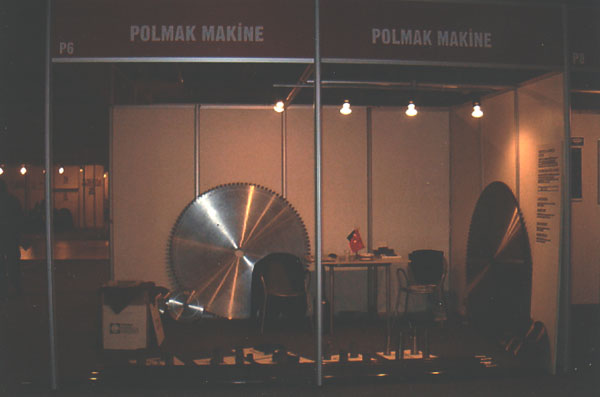
3. CIRCULAR SAW BLADE
PRODUCTS
DIA
mm |
SEGMENT QUANTITY |
SEGMENT SIZE |
DISC THICKNESS |
BORE DIA |
FLANGE DIA (mm) |
MOTOR RATING kw |
FLUSHING WATER lt/min |
DISC WEIGHT (kg) |
W |
H |
L |
250 |
15 |
2.2 |
7 |
40 |
1.6 |
30 |
100 |
5.5-7.5 |
6-10 |
0.6 |
300 |
21 |
3.4 |
7 |
40 |
1.8 |
60 |
120 |
7.5-11 |
10-15 |
1 |
350 |
25&27 |
3.4 |
7 |
40 |
2.2 |
60 |
140 |
7.5-11 |
10-15 |
1.6 |
400 |
28 |
3.8 |
7 |
40 |
2.5 |
60 |
150 |
7.5-11 |
10-15 |
2.5 |
450 |
32 |
4 |
7 |
40 |
2.8 |
60 |
160 |
11-15 |
15-20 |
3.4 |
500 |
36 |
4 |
7 |
40 |
2.8 |
60 |
170 |
11-15 |
20-30 |
4.1 |
600 |
36&42 |
4.6 |
7 |
40 |
3.5 |
60 |
180 |
15-18.5 |
30-35 |
7.5 |
650 |
39 |
5.8 |
7 |
40 |
4 |
60 |
200 |
15-20 |
30-35 |
10 |
725 |
50 |
5.8 |
7 |
40 |
4 |
60 |
200 |
18-22 |
30-35 |
12.6 |
800 |
46&57 |
5.8 |
7 |
40 |
4.5 |
60 |
225 |
25-30 |
30-40 |
17 |
850 |
50 |
6.5 |
7 |
40 |
4.5 |
60 |
240 |
25-30 |
30-40 |
19.5 |
900 |
64 |
5.8 |
7 |
40 |
5 |
80 |
250 |
30-37 |
30-40 |
25 |
1000 |
70 |
7.5 |
7.5 |
24 |
5 |
100 |
270 |
35-45 |
40-50 |
30 |
1100 |
74 |
8 |
8 |
24 |
5.5 |
100 |
300 |
35-45 |
40-50 |
40 |
1200 |
80 |
8 |
8 |
24 |
5.5 |
100 |
300 |
35-45 |
50-60 |
47.5 |
1300 |
88 |
9 |
9 |
24 |
6 |
120 |
300 |
40-45 |
50-60 |
60 |
1400 |
92 |
9 |
9 |
24 |
6.5 |
120 |
325 |
45-75 |
60-70 |
77 |
1600 |
104 |
9 |
9 |
24 |
6.5 |
120 |
375 |
45-75 |
60-70 |
100 |
1700 |
110 |
10 |
10 |
24 |
7 |
120 |
390 |
45-75 |
60-70 |
121 |
1750 |
112 |
10 |
10 |
24 |
7 |
120 |
400 |
55-75 |
70-80 |
129 |
1800 |
120 |
10 |
10 |
24 |
7 |
120 |
400 |
|
70-80 |
140 |
2000 |
132 |
11 |
10 |
24 |
8 |
120 |
425 |
55-75 |
70-80 |
197 |
400 ST |
24 |
5.8 |
7 |
40 |
3.5 |
60 |
18 |
13-15 |
15-20 |
3.2 |
450 ST |
26 |
5.8 |
7 |
40 |
3.5 |
60 |
20 |
13-15 |
15-20 |
4.6 |
500 ST |
30 |
5.8 |
7 |
40 |
3.5 |
60 |
24 |
15-17 |
18-20 |
5.4 |
Contact Us for the unspecified
segment dimensions.
PROBLEMS, CAUSES, REMEDIES
PROBLEM |
CAUSE |
REMEDY |
BLADE WILL NOT CUT |
Bad spindle bearings,
worn mounting arbor, or misaligned shaft.
V-belt is not tighten
properly, or insufficient power to permit blade to cut properly.
Blade has become dull, or
segments are broken.
|
Replace the worn parts.
Tighten belts in
accordance with machine maintenance instructions. Use correct voltage at
motor and use adequate horsepower for the cutting application.
Allow blade to sharpen
itself on the material to be cut when first placing it on the saw. |
LOSS OF TENSION |
Blade blank has been
overheated.
Blade blank has been
overheated as a result of blade spinning on mounting arbor.
High penetration rate
|
Provide proper amount of
water to both sides of blade. Check to make sure water pump is producing
sufficient water and that no blockages occur in water lines.Properly align
saw to permit square cutting. Avoid twisting the blade in cut. Make certain
that shaft r.p.m. is correct, so that blade operates at its tensioned speed,
and consequently runs perfectly straight.
|
UNEVEN SEGMENT WEAR |
Insufficient water,
generally on one side of the blade, which reduces side clearance.
Equipment defecet, which
causes the blade to wear out of round unevenly.
Saw head misaligned. |
Flush water system. Make
certain that water is being adequately and equally distributed to both sides
of the blade. Replace bad bearings, worn arbor shaft, or misaligned spindle.
Make certain the engine runs smoothly, to prevent harmonic vibrations, which
in turn cause the blade to pount on a regular cycle basis.
Check saw head alignment
for squareness both vertically and horizontally. |
SHORT LIFE |
Using the wrong blade on
a specific material. Inadequate water to the blade.
Flushing water quantity
is inadequate. |
Use the proper blade
specification, as recommended by the manufacturer.
Use sufficient water to
flush fines out of cut. If generated fines are highly abrasive, wear-retardant
steel cores should be used. Make sure water hoses are clean and free from
any blockages. Flush water system. Make certain that water is being
adequately and equally distributed to both sides of the blade
|
SEGMENT LOSS |
Overheating, due to
inadequate supply of water or complete loss of water.
Defective flange which
cause the blade to flutter in the cut or fail adequately support the blade
in perfect alignment.
|
Use sufficient water to
flush fines out of cut. If generated fines are highly abrasive, wear-retardant
steel cores should be used. Make sure water hoses are clean and free from
any blockages. Flush water system. Make certain that water is being
adequately and equally distributed to both sides of the blade
Clean foreign material
from blade clamping disc surfaces, or replace clamping if they are under
manufacturer’s recommended diameter. |
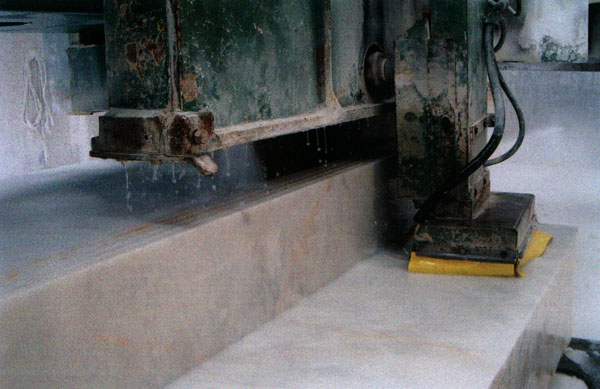
FRAME SAW BLADES
Polmak frame saw blades are manufactured from the highest quality alloy steel.
Polmak can design diamond frame saw segments for all your cutting applications.
These segments are brazed under precise temperature control by induction to
prevent any deformation of the steel body.
Frame saw blade dimensions are 3.5 mm thickness and 180 mm lenghts.
Segment dimensions:
1.
Standard type : 5 mm x 7 mm x 20 mm
2. Trapezoid type
: 5.5 mm x 7 mm x 20 mm (all diamond)
MASONERY MATKAPLAR
ÇAP , mm
|
Karot boyu |
DişTipi |
Soket Ölçüleri |
L |
W |
X |
30 |
400
|
R ½” |
10 |
5
|
7
|
40 |
50 |
60 |
70 |
80 |
I ¼” UNC |
90 |
100 |
110 |
120 |
|